В настоящее время в мире резко увеличилось использование вакуумных испарителей для очистки сточных вод в различных отраслях промышленности. Это связано с их экономичностью, автономностью функционирования и удобством обслуживания. Кроме того, созданные на их базе технологические участки занимают мало рабочего пространства.
Технология выпаривания для разделения растворов и выделения влаги широко применяется в химической промышленности. Однако традиционные системы нуждаются в достаточно сложном оборудовании и высоких энергозатратах, что делает их использование для очистки или концентрации растворов в большинстве случаев нерентабельным. Кроме того, обычно используемые при этом паровые компрессоры работают при высоких температурах и давлении, что приводит к образованию накипи и коррозии.
Поэтому в последнее время широкое распространение стали получать вакуум-выпарные установки (ВВУ), которые позволяют создавать автономные системы, обеспечивающие более мягкий процесс дистилляции, большой объем вырабатываемой воды, высокую степень концентрации и значительное снижение расхода энергии по сравнению с обычными испарителями. Принципиальная схема работы вакуум-выпарные установки представлена на рис.1.
Рис.1. Технологическая схема вакуум-выпарной установки:
1 - компрессор; 2 - камера кипения (дистилляционный куб); 3 - камера конденсации; 4 - емкость для дистиллята; 5 - эжектор (трубка Вентури); 6 - насос откачки концентрата; 7 - вакуумный (водокольцевой) насос; 8 - теплообменник (чиллер); 9 - рабочий резервуар.
Конструкция вакуумных испарителей ЭКОПРИМА базируется на проверенной технологии теплового насоса, объединенного с вакуумным. С помощью последнего обеспечивается создание вакуума в рабочем резервуаре (9) с остаточным давлением около 40 мбар. Точкой кипения воды при этом является температура около 30 °С. Необходимые тепло и холод обеспечиваются интегральным тепловым насосом (1), который сжимает газовую смесь (хладагент), нагревая ее до температуры около 70 °С. Сжатый газ прокачивается в змеевик и нагревает камеру кипения (2). При его погружении в концентрируемую жидкость он практически полностью передает тепло сжатого газа этой жидкости, которая начинает кипеть в дистилляционном кубе.
Работа вакуум-выпарной установки:
После передачи тепла в камере кипения происходит дальнейшее охлаждение хладагента, эта задача доводится до завершения воздушным (чиллер) или водяным охладителем теплообменника (8). После отдачи остатков тепла хладагент перемещается в змеевик конденсационной камеры (3), где расширяется и «генерирует» холод. Водяной пар, образовавшийся в камере кипения, движется к холодной зоне камеры (3), где конденсируется при контакте с холодной поверхностью змеевика. По мере накопления жидкость высасывается струйным насосом (5) и перемещается в накопитель дистиллята (4), где происходит вакуумный цикл: создание вакуума 30–40 мбар остаточного давления внутри камеры кипения и давления около 0,2 бар внутри накопителя дистиллята. Полученный дистиллят возвращается в технологический процесс на повторное использование. Степень концентрации остатка в дистилляционном кубе контролируется по времени либо измерителем плотности. После завершения процесса выпаривания концентрат удаляется из аппарата автоматически при помощи насоса (6). Далее концентрат либо возвращается в технологический цикл, либо сдается на утилизацию. Компрессор самосмазывающийся и закольцован в замкнутую систему с хладагентом.
Основные технико-экономические преимущества вакуум-выпарных установок ЭКОПРИМА:
• нет потребности в корректировке pH перед подачей раствора на выпаривание;
• в 1,5-2 раза снижены энергозатраты за счет создания глубокого вакуума;
• полностью автоматическая, почти непрерывная работа;
• выпаривание и конденсация с помощью теплового насоса;
• дистилляционный куб выполнен из титана ВТ 1-0;
• вертикальное или горизонтальное расположение рабочих резервуаров;
• контроллер Siemens с визуализацией процесса.
Вакуум-выпарные установки серии CR–TR с нагревательным кожухом либо змеевиком разработаны для доведения концентрата до сухой - кристаллические соли либо сметанообразной консистенции. ВВУ данной серии оборудованы миксером (скребком), который перемешивает концентрат и сохраняет нагревательный элемент в чистоте. Это позволяет упростить эксплуатацию установки и повысить степень концентрации. Концентрат удаляется через откидную створку в коническом днище выпарного куба с помощью миксера (скребка). Расположение рабочих резервуаров в данном случае - горизонтальное.
Стандартные модели с кристаллизатором солей имеют производительность от 150 до 3 000 литров дистиллята в сутки, возможно увеличение мощности благодаря модульности исполнения ВВУ.
Рис.2. ВВУ производительностью 2500 л/сутки со встроенным кристаллизатором солей. Энергопотребление данной установки составляет 120–150 Вт/л дистиллята.
Если на рабочем участке возможно нагревание и охлаждение рабочего резервуара с помощью пара и холодной воды, то можно отказаться от теплового насоса и, таким образом, значительно снизить энергопотребление выпарной установки до 10–20 Вт/л дистиллята. При этом значительно упрощается конструкция вакуумного выпаривателя.
Сегодня ВВУ успешно применяются при обработке металлов. С их помощью очищают воду и концентрируют расщепленные эмульсии, насыщенные растворы, растворы отработанных электролитов, сточные воды после вибрационного измельчения, после пресс-литья (отделение составляющих, смазок), восстанавливают стоки от стационарных промывочных устройств, утилизируют солевой концентрат с обратноосмотических мембранных установок на стациях ХВО ТЭЦ.
В гальваническом производстве ВВУ концентрируют отработанные растворы нанесения покрытий и возвращают на повторное использование промывные воды, утилизируют драгоценные металлы, регенерируют растворы кислот и щелочей.
Наиболее успешно вакуум-выпарные аппараты применяются в системах обработки концентрированных промывных вод после ванн нанесения гальванических покрытий, причем целью выпаривания является не получение твердого продукта, а увеличение концентрации компонентов в промывной воде до их содержания в ванне покрытия. В этом случае промывную воду можно вернуть в ванну покрытия (например, хромирования или никелирования) и сделать технологию нанесения покрытий практически безотходной. Затраты на проведение процесса окупаются за счет экономии возвращаемых материалов и экономии химических реагентов на обезвреживании стоков. Важно отметить, что низкая температура кипения в ВВУ (30 °С – 40 °С) позволяет избежать разложения органических добавок, содержащихся в электролитах.
Рис.3. Технологическая схема применения ВВУ в гальваническом производстве.
Метод наиболее эффективен, если выпариванию подвергается промывная вода после многоступенчатой каскадной промывки. Это объясняется тем, что объем такой воды минимален, а концентрация компонентов – максимальна. Производительность выпарной установки должна соответствовать расходу воды на промывку.
Наиболее успешным с экологической точки зрения является использование ВВУ в оборотных системах водоснабжения. Система работает в автономном режиме под наблюдением одного оператора, функции которого заключаются в запуске установки в начале рабочей смены и выключении в конце рабочей смены. Поскольку ВВУ может работать круглосуточно в режиме 24/7, наиболее целесообразно как с точки зрения капитальных затрат на приобретение оборудования, так и с точки зрения экономии электроэнергии её использование в постоянном режиме. Для постоянного режима работы ВВУ укомплектовывается накопительным резервуаром для создания равномерного расхода утилизируемых сточных вод.
Технология выпаривания для разделения растворов и выделения влаги широко применяется в химической промышленности. Однако традиционные системы нуждаются в достаточно сложном оборудовании и высоких энергозатратах, что делает их использование для очистки или концентрации растворов в большинстве случаев нерентабельным. Кроме того, обычно используемые при этом паровые компрессоры работают при высоких температурах и давлении, что приводит к образованию накипи и коррозии.
Поэтому в последнее время широкое распространение стали получать вакуум-выпарные установки (ВВУ), которые позволяют создавать автономные системы, обеспечивающие более мягкий процесс дистилляции, большой объем вырабатываемой воды, высокую степень концентрации и значительное снижение расхода энергии по сравнению с обычными испарителями. Принципиальная схема работы вакуум-выпарные установки представлена на рис.1.
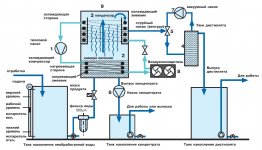
1 - компрессор; 2 - камера кипения (дистилляционный куб); 3 - камера конденсации; 4 - емкость для дистиллята; 5 - эжектор (трубка Вентури); 6 - насос откачки концентрата; 7 - вакуумный (водокольцевой) насос; 8 - теплообменник (чиллер); 9 - рабочий резервуар.
Конструкция вакуумных испарителей ЭКОПРИМА базируется на проверенной технологии теплового насоса, объединенного с вакуумным. С помощью последнего обеспечивается создание вакуума в рабочем резервуаре (9) с остаточным давлением около 40 мбар. Точкой кипения воды при этом является температура около 30 °С. Необходимые тепло и холод обеспечиваются интегральным тепловым насосом (1), который сжимает газовую смесь (хладагент), нагревая ее до температуры около 70 °С. Сжатый газ прокачивается в змеевик и нагревает камеру кипения (2). При его погружении в концентрируемую жидкость он практически полностью передает тепло сжатого газа этой жидкости, которая начинает кипеть в дистилляционном кубе.
Работа вакуум-выпарной установки:
После передачи тепла в камере кипения происходит дальнейшее охлаждение хладагента, эта задача доводится до завершения воздушным (чиллер) или водяным охладителем теплообменника (8). После отдачи остатков тепла хладагент перемещается в змеевик конденсационной камеры (3), где расширяется и «генерирует» холод. Водяной пар, образовавшийся в камере кипения, движется к холодной зоне камеры (3), где конденсируется при контакте с холодной поверхностью змеевика. По мере накопления жидкость высасывается струйным насосом (5) и перемещается в накопитель дистиллята (4), где происходит вакуумный цикл: создание вакуума 30–40 мбар остаточного давления внутри камеры кипения и давления около 0,2 бар внутри накопителя дистиллята. Полученный дистиллят возвращается в технологический процесс на повторное использование. Степень концентрации остатка в дистилляционном кубе контролируется по времени либо измерителем плотности. После завершения процесса выпаривания концентрат удаляется из аппарата автоматически при помощи насоса (6). Далее концентрат либо возвращается в технологический цикл, либо сдается на утилизацию. Компрессор самосмазывающийся и закольцован в замкнутую систему с хладагентом.
Основные технико-экономические преимущества вакуум-выпарных установок ЭКОПРИМА:
• нет потребности в корректировке pH перед подачей раствора на выпаривание;
• в 1,5-2 раза снижены энергозатраты за счет создания глубокого вакуума;
• полностью автоматическая, почти непрерывная работа;
• выпаривание и конденсация с помощью теплового насоса;
• дистилляционный куб выполнен из титана ВТ 1-0;
• вертикальное или горизонтальное расположение рабочих резервуаров;
• контроллер Siemens с визуализацией процесса.
Вакуум-выпарные установки серии CR–TR с нагревательным кожухом либо змеевиком разработаны для доведения концентрата до сухой - кристаллические соли либо сметанообразной консистенции. ВВУ данной серии оборудованы миксером (скребком), который перемешивает концентрат и сохраняет нагревательный элемент в чистоте. Это позволяет упростить эксплуатацию установки и повысить степень концентрации. Концентрат удаляется через откидную створку в коническом днище выпарного куба с помощью миксера (скребка). Расположение рабочих резервуаров в данном случае - горизонтальное.
Стандартные модели с кристаллизатором солей имеют производительность от 150 до 3 000 литров дистиллята в сутки, возможно увеличение мощности благодаря модульности исполнения ВВУ.
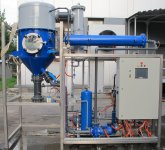
Если на рабочем участке возможно нагревание и охлаждение рабочего резервуара с помощью пара и холодной воды, то можно отказаться от теплового насоса и, таким образом, значительно снизить энергопотребление выпарной установки до 10–20 Вт/л дистиллята. При этом значительно упрощается конструкция вакуумного выпаривателя.
Сегодня ВВУ успешно применяются при обработке металлов. С их помощью очищают воду и концентрируют расщепленные эмульсии, насыщенные растворы, растворы отработанных электролитов, сточные воды после вибрационного измельчения, после пресс-литья (отделение составляющих, смазок), восстанавливают стоки от стационарных промывочных устройств, утилизируют солевой концентрат с обратноосмотических мембранных установок на стациях ХВО ТЭЦ.
В гальваническом производстве ВВУ концентрируют отработанные растворы нанесения покрытий и возвращают на повторное использование промывные воды, утилизируют драгоценные металлы, регенерируют растворы кислот и щелочей.
Наиболее успешно вакуум-выпарные аппараты применяются в системах обработки концентрированных промывных вод после ванн нанесения гальванических покрытий, причем целью выпаривания является не получение твердого продукта, а увеличение концентрации компонентов в промывной воде до их содержания в ванне покрытия. В этом случае промывную воду можно вернуть в ванну покрытия (например, хромирования или никелирования) и сделать технологию нанесения покрытий практически безотходной. Затраты на проведение процесса окупаются за счет экономии возвращаемых материалов и экономии химических реагентов на обезвреживании стоков. Важно отметить, что низкая температура кипения в ВВУ (30 °С – 40 °С) позволяет избежать разложения органических добавок, содержащихся в электролитах.
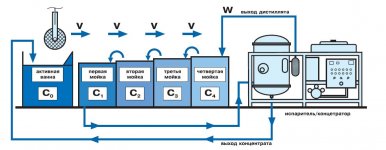
Метод наиболее эффективен, если выпариванию подвергается промывная вода после многоступенчатой каскадной промывки. Это объясняется тем, что объем такой воды минимален, а концентрация компонентов – максимальна. Производительность выпарной установки должна соответствовать расходу воды на промывку.
Наиболее успешным с экологической точки зрения является использование ВВУ в оборотных системах водоснабжения. Система работает в автономном режиме под наблюдением одного оператора, функции которого заключаются в запуске установки в начале рабочей смены и выключении в конце рабочей смены. Поскольку ВВУ может работать круглосуточно в режиме 24/7, наиболее целесообразно как с точки зрения капитальных затрат на приобретение оборудования, так и с точки зрения экономии электроэнергии её использование в постоянном режиме. Для постоянного режима работы ВВУ укомплектовывается накопительным резервуаром для создания равномерного расхода утилизируемых сточных вод.
Последнее редактирование: